
DLyte PRO500
Automated Cell
Full automation to integrate surface finishing in production lines
DLyte PRO500®AUTOMATED CELL is the ultimate solution for industries requiring full automation —or a multi-level DLyte process automation— to integrate surface finishing in production lines.
​
This system allows customers to automate the process of loading and unholding holders into and from the machine, in order to increase the overall cell productivity working autonomously for a longer time and reducing the loading and unloading times.
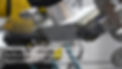
General Automation Benefits


Load parts to the 8 holders
Load 8 holders on the machine
Polishing process
Unload 8 holders from the machine
Unload parts from the 8 holdes
Cycle time


Less manpower
Improve productivity with fully automated process cycle
Effective solution to bottle neck production with a safety buffer supply
Up to 8 cycles
working autonomously

Benefits of DLyte PRO500 Automated CELL
-
Take advantage of the First In Out (FIFO) production control
-
It allows to begin to work with one DLyte PRO500 machine, and add a second one later
-
Pristine machine efficiency, due to the specially designed double gripper for fast exchange cycle
-
High increase in production with 64 holders
-
Easily automated with a smart control panel
-
Load & Unload sequence and separate robot workflows
-
Plug & Play solution of polishing and automation
Equipment Configuration
-
Fully automated
-
Increased output (24/7)
-
Multi-process step automation
-
Low operating costs
-
Remote servicing
-
It minimizes human error
-
Reliable lead time


Loading & Unloading Station
The carousel is a steel structure in a square-shaped designed to hold up to 64 holders in total. It can pivot above its bedplate, stopping after each ¼ round to allow the robot to work on the holder rows.
Once the robot is working one side of the carousel, the operator can simultaneously load and unload on the opposite side of it.
Workflow Description
The robot is a standard FANUC robot of 50 kg (about 110 lbs), with a double gripper at the end designed to hold two holders at once. By doubling the holders, the robot can load the unpolished holder into the machine and extract the polished one and place it on the carousel, all in one sequence.

How it Works
(1 Polishing Machine)
Full
The operator sets up the system to work continuously until all the parts in the carousel have been polished. Once finished, the user can unload them all. (Different recipes can be used for selected rows).
Continuous
The user replaces the visible face of the carousel (16 holders) while the opposite is being polished. This allows the operator to replace the polished parts with raw parts while the machine.

How it Works
(2 Polishing Machines)
Double Throughput
If two DLyte PRO500 machines are being used, the operator is able to increase production by cutting in half production time. Thus, increasing output with an ultra-low footprint.
2-Step processes
Combine different electropolishing processes, including different media for the same pieces in order to fully automate two-step polishing process, among other options.

Control Panel
The control panel located on the right front side, allows the user to control all the functions, both the cell and the DLytePRO500 outside the processing area.
​
The cell has a complete loading manager where the operator can set the automation cycle, depending on the batch, row and polishing recipe.
​
The mirror function allows the operator to access the Human-Machine Interface (HMI) of the DLyte PRO500 to operate directly on the machine.
Layout and Guarding
The front side is used to access the loading and unloading holder process. The front open fence (F) is protected with a safety light curtain. At the rear side (R) there is a hinge door. This area is permanently locked and can only be accessed during maintenance.
The pole located in the front area, has a floor and laser scanner that automatically stops the polishing process in case the operator accesses the area unannounced, thus achieving a high safety standard.

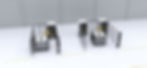
Get a quotation

DLyte PRO500 Automated Cell has been developed with the support of the European Union's Horizon 2020 grant for research and development of the DLytePRO range.