Respects the tolerances and initial shapes
Increases resistance to corrosion
Easier,
faster and cost-efficient
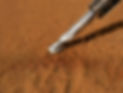
A solution for each material and geometry
DLyte simplifies and standardizes the post-process of metal parts, improving the finishing results obtained with traditional systems.
Provides a solution to the most common industrial metals and alloys. Its applications range from grinding, rounding and deburring to surface smoothing and high gloss polishing of high precision and aesthetic parts.
Automated system that improves the results of hand polishing
Metallic parts used for high-precision applications within the industrial sector must satisfy strict geometrical tolerances and present reduced roughness at microscopic level to ensure minimum friction, exact coupling and high wear and failure resistance.
These include increased corrosion resistance, fatigue resistance, resistance to erosion and premature aging, excellent biocompatibility, and improved adherence of subsequent coatings and better appearance and brightness.

How it works

Step 1
The parts are
clamped onto
the holder
Step 2
The holder is
introduced into
the machine
Step 3
The program
is selected
Step 4
Average of 50-60
minutes per cycle
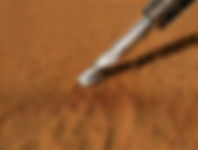
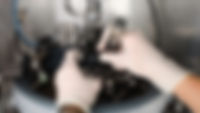



Before DLyte
60 minute cycle time

After DLyte
It provides a solution to the most common industrial metals and alloys. The applications for DLyte range from grinding, rounding and deburring to surface smoothing and high gloss polishing of high precision and aesthetic parts.
.png)

Cobalt Chrome
Stainless Steel
Carbon Steel
Carbides
Nickel Alloys
Aluminium Alloys
Copper Alloys
Titanium Alloys

“DLyte performs at least two times better surface quality than the next-best alternative post-processing technologies”.
Analyzed by Fraunhofer IAPT.
Non abrasive polishing
DLyte is the first non abrasive surface finishing system able to reduce substantially the roughness. Being a non abrasive process allows to reduce the roughness keeping the initial shapes and respecting the tolerances.
Additive manufacturing
Additive manufacturing is one of the most disruptive technologies with a wide range of applications in the industry. However, one of the barriers to the AM industry growth is the surface quality achieved.
The combination of AM and DLyte enables the use of AM for high precision applications where coupling and wear and failure resistance become critical.
Mirror finishing in one step
DLyte achieves fully automated polishing to a mirror finish in one step, while mechanical surface finishing requires several steps to achieve mirror finishing and liquid electropolishing generally reduces surface roughness readings of a non-electropolished surface by only 50%.
Enhance corrosion resistance
Corrosion is one of the main factors reducing the lifespan of mechanical parts. Most applications require a surface treatment to be performed after polishing to comply with the corrosion resistance requirements of the industry.

DLyte is the only system able to remove roughness substantially and improve the corrosion resistance of the metal pieces while at the same time reducing the number of processes required in the manufacturing process.
DLyte achieves better corrosion resistance than liquid electropolishing. The dry electropolished sample analyzed has lower surface roughness and more luster than the liquid electropolished sample.

“DLyte achieves better
corrosion resistance than
liquid electropolishing”.


Fragile parts finishing
The part with fine geometries require high-quality surface finishing with the disadvantage of requiring a non-aggressive process to avoid damages caused by mechanical energy. DLyte is suitable for these applications as it is an electrochemical process.
Compared to liquid electropolishing, DLyte is more controllable and works efficiently at micro and macroscopic level.
Time saving and lower cost production
An automatic process which reduces the complexity of the current multi-step processes, reducing labor costs and eliminating the need to rework parts and the production of defective parts.

Easy waste management
and low waste and water consumption
DLyte is a clean, non-hazardous process. It does not generate dust or noise and replaces manual surface finishing processes related to occupational diseases. By reducing the traditional multi-step process, DLyte improves working conditions, and drastically reduces the toxicity of the current polishing.
Improvement of the working environment
The DLyte process does not require any rubber tip, electrolytic bathing or brushing, but just a simply abrasive preparation beforehand. By reducing the traditional multi-step process, DLyte improves working conditions, and drastically reduces the toxicity of the current polishing.

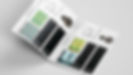