
DLyte 10,000
Modular solutions
for mass production

Robot Configuration
Installation for challenging industries with comples geometries.
​
# Aeronautics, Industry with big parts production.
Wide Range of Materials
DLyte10,000 delivers the full range of electrical parameters, from low to high frequency, parameter concatenation and asymmetric voltage.
​
In addition, it allows the user to search the ideal parameters for its pieces in the library of processes in the Polishing Manager APP.

Cobalt Chrome
Stainless Steel
Carbon Steel
Carbides
Nickel Alloys
Aluminium Alloys
Copper Alloys
Titanium Alloys


100 kg
Large and Heavy Workpieces
The range of applications for the DLyte10,000 are workpieces from the aerospace, energy, oil and gas, shipbuilding, machinery and food industries.
DLyte10,000 is the perfect system for large and heavy workpieces with a diameter of up to 750 mm and length of up to 600 mm and a maximum weight of 100 kg.
Complex Geometries
DLyte10,000’s robot module is designed to polish complex geometries, which could not reach targeted surface finishing without a 6-axis movement.



Single and Multiple Workpiece Holders
The work piece holders or fixtures containing the work pieces are specially designed to optimize the results based on the piece geometry and finishing requirements. The large adaptability of the holding systems ensures capacity optimization for several applications and versatility to use one machine for a wide range of pieces.
Best-in-class Performance and Repeteability
The new reliable electronics provide better surface finishes, more homogeneous results and shorter cycle times, by optimizing the parameters, process combinations, applying asymmetric pulses, and creating multiple movements.
Repeatability and high precision, is achieved with innovative power electronics, using the new SIC Pulser technology, with 8 independent high-frequency rectifiers synchronized by fiber optic cables, delivering up to 55 kW.
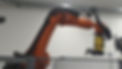
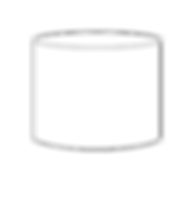
Large parts:
750 Ø mm x 600 mm
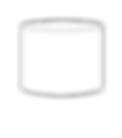
Middle-size parts:
400 Ø mm x 350 mm
Small parts:
250 Ø mm x 200 mm

Multiple Movement Combinations
The mechanical systems of the DLyte10,000 are robust, precise and reliable, designed for mass production. They enable the perfect combination of multiple movements and vibrations, maximizing its performance.
The machine offers different presetting robot movements for three size ranges:
​
Large parts: 750 Ø mm x 600 mm
Middle-size parts: 400 Ø mm x 350 mm
Small parts: 250 Ø mm x 200 mm
Automatic Workpiece Loading and Unloading
The integrated automatic loading system ensures ergonomic workpiece loading and unloading with a safety size tool.


Project Development, Integration and Set-Up
We support with engineering services, development of surface finishing processes, machinery definition, integration, set up, training, on-site consulting and services in the digital field to enhance machine availability and optimize manufacturing processes.
Easy waste management
and low waste and
water consumption
The DLyte system does not require closed-up system to recycle water and sludge waste treatment machinery with the corresponding space, labor, water and environmental license costs savings. The disposal of the dry electrolyte is handled by standard services.

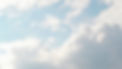
Improvement of the working environment
The DLyte process does not require any rubber tip, electrolytic bathing or brushing, but simply an abrasive preparation beforehand. By reducing the traditional multi-step process, DLyte improves working conditions, and drastically reduces the toxicity of the current polishing.
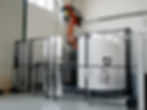