
DLyte eBlast
Electro Blasting Surface Finishing
DLyte eBlast is a new equipment that provides a stream of solid-electrolyte particles propelled by a non-conductive liquid media to improve surface quality of metal parts using the patented electro blasting technology.
Electro Blasting is an electrochemical metal surface finishing process especially designed to treat to a mirror finish metal parts with complex geometries. This system is also suitable for large or heavy parts which are difficult to polish by immersion or that require a localized surface finishing.
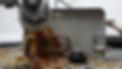

Electro-Blasting's Benefits
Molds
eBlast is able to mirror finish molds with functional and cosmetic applications. It performs high standard for surface flatness, smoothness and geometric precision in molds. it is useful for molds with cavities, slots, and occluded areas, overcoming its weight and size limitations.​

Welded Parts
Parts get a chrome-like appearance and finish without high costs and environmental disadvantages. Pieces are naturally passivated, have an improved resistance to corrosion, and have no stressed or disturbed layers of surface metal caused by welding, cutting, or mechanical finishing.

Cavities
It is able to polish parts with cavities and narrow spaces such as blind holes, slots, corners and occluded areas, by focusing the media stream towards the targeted area from a very short distance, and by protecting the surface from pitting.​

Complex Geometries
​Internal surfaces of complex geometries can be easily treated as the stream of electrolyte and current can be effectively directed to the target surface. This improves the results obtained with abrasive polishing and electropolishing, where some surfaces become unpolished.

Inner Channels
Straight inner channels and with open angles with a minimum diameter of 20 mm can be effectively polished. With the flexible nozzles and diffusers, inner surfaces can be treated as the electrode is located at the tip of the nozzle. The surface remains protected and clean, as the high viscosity of the media flows through the cavities maintaining the particle’s connectivity.

Delicate and Fragile Parts
Delicate and fragile parts can be finished without being harmed as the process does not use vibration nor strong mechanical forces. As the media stream has low pressure, pieces can be electrically connected without a tight fixation.

Electro Blasting Process
Electro blasting uses a jet of fluid composed by a non-conductive liquid and free solid polymer particles to remove roughness from the metal surfaces. As particles contact the surface selectively on roughness peaks, only those peaks get electrochemically eroded, producing an overall polishing effect.
​
The non-electrically conductive liquid is not directly involved in the electropolishing process. Its main function is to carry the particles, but also to maintain the connectivity and conductivity between particles during the process. Specially in roughness valleys, the liquid forms a protective layer over the metallic surface to avoid pitting.

vs. DryLyte Technology
The gas in the interstitial space (the space between the particles) has been replaced by a non-conducting liquid. The granular state of the media becomes fluid, so it can be pumped, projected, collected, etc. which open a wide range of possibilities.
vs. Abrasive
Electro Blasting does not use high pressure to remove roughness. Its electrochemical process only polishes conductive surfaces. This process protects the material, and if desired it generates a passive layer. ​
Advantages over abrasive:
-
Does not stress the surface and either cause scratches over smooth surfaces
-
Does not produce inclusions on the metal surfaces and either create dust remnants or noise
-
Safer than abrasive blasting, by not creating breathing difficulties, or risk of rebounded injuries
The equipment comprises different guns and
nozzles to achieve targetd surface finishing
depending on the geometry and application.
​
The distance of application of the jet differs
between materials with a maximum distance
of 100 mm for stainless steel and cobalt-chrome
(CoCr) and 20 mm for titanium and carbon steel.
​
The turntable system increases comfort, and productivity while decreasing the overall operator’s fatigue. By placing the part on the turntable, and manually spinning it while electro-blasting it, saves time and effort from lifting and turning heavy parts.
​
The work area has been designed to hold 300 kg and a maximum piece volume of 1,000 x 500 x 500 mm.
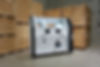

How it Works
The eBlast equipment comprises two systems:
Recirculating System
It pumps the electrolytic media (liquid plus particles) through the eBlast gun to the working cabin. The user controls this stream and can direct it to the relevant areas to polish. The eBlast gun hosts an electrode so that the particles coming out from the nozzle have electrical connectivity.
Electric System
It comprises a power source that is connected to the piece to polish and to the electrode in the nozzle. The current that the power source provides can be tuned by different parameters for each metal and alloy, which is a key parameter of a successful polishing result. The current flows in the close circuit are established between power source—electrode—particles—surface.

