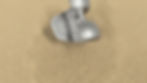
Success cases
Industrial

Dry electropolishing of mixers & agitators
For Processed Foods, Dairy, Beverages, Pharmaceutical & Biotech Industries
Food industry requires specific materials, design and surface quality to fulfill the standards of the industry in terms of durability, compatibility, homogeneity and cleanability. Dry electropolishing provides numerous advantages as it improves surface quality while reducing the number of process steps and costs. It precisely removes surface roughness, preserves geometry and tolerances, extends the lifespan of parts improving the corrosion resistance and prevents bacteria growth.
​
This success case explains how a manufacturer of mixers and agitators for food industry improved the quality of the products while reducing the cost and environmental impact using DLyte Dry electropolishing process. The company replaced manual polishing and outsource of traditional electropolishing only by dry electropolishing. In this document, you will discover why dry electropolishing is the preferred process for improving surface quality of metal agitators and mixers. And also you will learn:
​
-
Why dry electropolishing is more effective than current methods
-
How dry electropolishing works
-
Benefits of dry electropolishing for food industry
-
Cost analysis of Dry electropolishing including CAPEX and OPEX
​
Download your free copy and learn how a manufacturer of mixers and agitators for the food industry improved the quality of its products and its profit.
Tablet punches manufacturing & refurbish
For the Pharma Industry
Within the tablet production field, the importance of a perfect appearance of the pills in a package is crucial to avoid doubts about integrity and quality of the product.
Dry electropolishing automates the polishing process, avoids imperfections in the surface or breakage of the tablets, improves the performance and extends the lifespan of the pressing tools, while reducing time, costs and environmental impact. It precisely automates surface finishing operations, preserves geometry, tolerances and biocompatibility.
This success case explains how a manufacturer of tablet punches improved the quality of the products while reducing time and costs using DLyte. The company replaced a multi-step process, including automated abrasive polishing and manual polishing using nylon and brass brushes with the DryLyte Technology.
In this document, you will learn why dry electropolishing is the preferred process for the surface finishing of tablet punches.
You will also learn:
​
-
Why dry electropolishing is more effective than current methods
-
How dry electropolishing works
-
Benefits of dry electropolishing for food industry
-
Cost analysis of Dry electropolishing including CAPEX and OPEX
​
Download your free copy and learn how a manufacturer of tablet punches improved the quality of its products and its profit.


Cap compression molding tools polishing
For Food, Beverage & Packaging Industries
Within the caps and closures production, the importance of a perfect appearance, functionality and repeatability is crucial. The surface quality of a cap compression mold tool affects productivity, quality and aesthetics of the end product: the closure.
Dry electropolishing prevents imperfections on the closure’s surface, performance reduction of the press due to longer press cycles, a short lifespan of the compression molds and sticking of the cap during decompression.
To reach the technical specifications of the surface and the lowest total process time and cost, our client implemented DLyte successfully, achieving high-gloss polishing of compression mold punches while decreasing friction, preventing cap adherence, premature failure and corrosion, while keeping tight tolerances.
In this document, you will find out why dry electropolishing is the preferred process for the surface finishing of cap compression molding tools.
You will also learn:
​
-
Why dry electropolishing is more effective than current methods
-
How dry electropolishing works
-
Benefits of dry electropolishing for the medical device industryy
-
Cost analysis of dry electropolishing, including CAPEX and OPEX
​
Download your free copy and learn how a manufacturer of cap compression molding tools improved the quality of its products and its profit.
Eyewear surface finishing
For Luxury & Lifestyle Industries
Within the eyewear production field, the importance of a perfect appearance of the piece is one of the key elements to assess the quality of the product. For many people, eyeglasses are used as jewelry and are the most expensive daily accessory. One of the differences between regular and luxury eyeglasses is the weight, since light glasses are more comfortable than heavy ones.
The DryLyte Technology allows achieving a perfect eyewear surface finishing, as it can treat small corners without changing geometries and preserving tolerances, keeping the existing logo, name, or sign unaltered. All of this can be achieved while maximizing the capacity per cycle in the DLyte equipment.
In this document, you will learn why dry electropolishing is the preferred process for the eyewear surface finishing.
​
You will also learn:
​
-
Why dry electropolishing is more effective than current methods
-
How dry electropolishing works
-
Benefits of dry electropolishing for luxury and lifestyle industries
-
Cost analysis of DLyte’s Dry electropolishing applied to a dental laboratory
​
Download your free copy and learn how a manufacturer of eyewear improved the quality of its products and its profit.
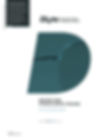

Injection molding polishing
For the mold and die industry
Injection molding manufacturing has evolved during the last years to improve the throughput, and quality of the manufactured parts, and to extend the useful life of the mold. The increased complexity in designs and materials has supposed a challenge for mold designers and manufacturers who are looking for new, more precise, and reliable processes.
The DryLyte Technology makes the polishing of molds without losing tolerances and radius precise and reliable. The DLyte process does not generate dust or heavy noise. Metals removed from the workpieces remain in the media, so workers are not exposed to noise or dust.
In this document, you will learn why dry electropolishing is the preferred process for the surface finishing of molds.
​
You will also learn:
​
-
Why dry electropolishing is more effective than current methods
-
How dry electropolishing works
-
Benefits of dry electropolishing for the mold and die industry
-
Cost analysis of dry electropolishing including CAPEX and OPEX
​
Download your free copy and learn how a manufacturer of molds improved the quality of its products and its profit.
Ultrahigh-purity valve inner channel polishing
For semiconductor, chemical, food and pharmaceutical industries
Demand for gas supplies and components with ultraclean surfaces has grown with the rising need for purity in the process medium. When manufacturing ultraclean gas-supply systems, leak-tight integrity, purging quality, purity, and lack of particles at its point of use needs to be ensured.
The DryLyte Technology allows achieving a perfect surface finishing of valve inner channel, as it is more precise and homogeneous than current abrasive processes as material removal is performed by an electrochemical process which depends on the number of impacts of the media against the surface. All of this is achieved while maximizing the capacity per cycle in the DLyte equipment.
In this document, you will learn why dry electropolishing is the preferred process for the surface finishing of the valve inner channel.
You will also learn:
​
-
Why dry electropolishing is more effective than current methods
-
How dry electropolishing works
-
Benefits of dry electropolishing for semiconductor, chemical, food and pharmaceutical industries
-
Cost analysis of DLyte’s Dry electropolishing applied to a dental laboratory
​
Download your free copy and learn how a manufacturer of valves improved the quality of its products and its profit.


Grinded carbide insert polishing
For Toolmaking Industry
The increasing complexity in designs and materials is a challenge for tool manufacturers who are looking for new processes in order to offer more precise and reliable cutting tools.
​
Dry electropolishing automates the polishing process, avoids imperfections in the surface, while reducing time, costs and environmental impact. It precisely automates surface finishing operations, preserves geometry, tolerances and biocompatibility.
​
This success case explains how a manufacturer of grinded carbide insert improved the quality cutting-edges and reduce cost of polishing of carbide inserts, with mirror surface finishing and a significant roughness reduction.
​
In this document, you will learn why dry electropolishing is the preferred process for surface finishing of grinded carbide insert.
You will also learn:
​
-
Why dry electropolishing is more effective than current methods
-
How dry electropolishing works
-
Benefits of dry electropolishing for the toolmaking industry
-
Cost analysis of dry electropolishing including CAPEX and OPEX
​
Download your free copy and learn how a manufacturer of grinded carbide insert improved the quality of its products and its profit.
Propellers, impellers & hydro turbines
For Marine & Energy Industries
As it is well known, the design, manufacturing, and surface finishing of marine propellers and hydro turbines have a big impact in the energy efficiency and the speed of the boat. Surface quality is a key factor so that the turbine or propeller can be cleaned easily and reliably to keep the surface free of marine organisms.
Dry electropolishing improves surface quality of marine propellers automates the polishing process, avoids imperfections in the surface, while reducing time, costs and environmental impact. It precisely automates surface finishing operations, preserves geometry, tolerances and biocompatibility.
​
This success case explains how a manufacturer of marine propellers, impellers, and hydro turbines improved the quality of its products while reducing the cost and environmental impact using DLyte.
​
In this document, you will learn why dry electropolishing is the preferred process for surface finishing of marine propellers.
​
You will also learn:
​
-
Why dry electropolishing is more effective than current methods
-
How dry electropolishing works
-
Benefits of dry electropolishing for the marine and energy industries
-
Cost analysis of dry electropolishing, including CAPEX and OPEX
​
Download your free copy and learn how a manufacturer of marine propellers, impellers, and hydro turbines improved the quality of its products and its profit.

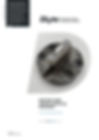
Carbide insert die
For toolmaking industry
Carbide inserts are replaceable bits of cemented carbide used in machining. The use of inserts allows faster machining and better finishes in metal parts, as they can withstand higher temperatures than high speed steel tools.
​
Polishing carbide insert dies is a resource-intensive activity, as it is based on manual polishing. Besides taking hours, it leads to non-satisfactory results.
​
Dry electropolishing automates the polishing process, avoids imperfections in the surface, while reducing time, costs and environmental impact. It precisely automates surface finishing operations, preserves geometry, tolerances and biocompatibility.
​
This success case explains how a manufacturer of carbide insert dies improved the production capacity and quality and reduce cost of polishing of carbide insert dies.
​
In this document, you will learn why dry electropolishing is the preferred process for surface finishing of carbide insert dies.
You will also learn:
​
-
Why dry electropolishing is more effective than current methods
-
How dry electropolishing works
-
Benefits of dry electropolishing for toolmaking industry
-
Cost analysis of dry electropolishing including CAPEX and OPEX
​
Download your free copy and learn how a manufacturer of carbide insert dies improved the quality of its products and its profit.
Carbide insert polishing
For toolmaking industry
The increased complexity in designs and materials has supposed a challenge for tool manufacturers who are looking for new processes in order to offer better, more precise and reliable cutting tools. The quality of a machined product, such as the dimensional accuracy and surface integrity, depends on many factors; for example, tool geometry, work material, and cutting conditions employed in the machining process.
​
Dry electropolishing automates the polishing process, avoids imperfections in the surface, while reducing time, costs and environmental impact. It precisely automates surface finishing operations, preserves geometry, tolerances and biocompatibility.
​
This success case explains how a manufacturer of carbide insert improved the production capacity and quality and reduce cost of polishing of carbide insert.
In this document, you will learn why dry electropolishing is the preferred process for surface finishing of carbide insert.
​
You will also learn:
​
-
Why dry electropolishing is more effective than current methods
-
How dry electropolishing works
-
Benefits of dry electropolishing for toolmaking industry
-
Cost analysis of dry electropolishing, including CAPEX and OPEX
​
Download your free copy and learn how a manufacturer of carbide insert improved the quality of its products and its profit.


Brass instruments
For musical instruments companies
Within the instrument production field, the importance of a perfect appearance of the piece is one of the key elements to assess the quality of the product. A perfect surface was only achievable with tedious and time-consuming manual processes which require high skills, space for workstations and suppose repetitive mechanical movements and toxic polishing compounds. The company continuously try to introduce production processes that to assure high-quality of its products and are safer for human health and environment.
​
Dry electropolishing improves surface quality of brass instruments, avoids imperfections in the surface, while reducing time, costs and environmental impact. It precisely automates surface finishing operations, preserves geometry, tolerances and biocompatibility and extends the lifespan of brass instruments while improving the corrosion resistance.
​
This success case explains how a manufacturer of brass instruments improved the production capacity and quality and reduce cost of polishing of brass instruments.
​
In this document, you will learn why dry electropolishing is the preferred process for surface finishing of brass instruments.
You will also learn:
​
-
Why dry electropolishing is more effective than current methods
-
How dry electropolishing works
-
Benefits of dry electropolishing for toolmaking industry
-
Cost analysis of dry electropolishing, including CAPEX and OPEX
​
Download your free copy and learn how a manufacturer of brass instruments improved the quality of its products and its profit.
Handle knives polishing
For the cookware industry
In the cookware production industry, it is essential for manufacturers to have high-quality polishing processes for their stainless-steel kitchen knives. The primary reason for this is to ensure proper surface finishing, which is crucial for maintaining hygiene. If knives are not polished correctly, it can lead to visible stains, dried fragments of food, and residue.
​
Moreover, the appearance of knives is vital for a manufacturer's corporate image. A mediocre finish can harm a manufacturer's branding, as polishing serves both a functional and an aesthetic purpose.
​
Dry electropolishing is an automated process that avoids surface imperfections, enhances performance, and extends the lifespan of knives while reducing time, costs, and environmental impact. It preserves geometry, tolerances, and biocompatibility by accurately automating surface finishing operations.
This success story details how a knife manufacturer improved production capacity and quality while reducing the cost of polishing knives using dry electropolishing.
​
This document explains why dry electropolishing is the preferred process for surface finishing handle knives and outlines its effectiveness, how it works, benefits for the cookware industry, and cost analysis, including CAPEX and OPEX.
​
Download your free copy and learn how a knife manufacturer improved the quality of its products and increased profit using dry electropolishing.


Carbide endmill
For the Toolmaking Industry
Cutting tools manufacturing have evolved during the last years to improve throughput and quality of machined parts, and to extend the useful life of the cutting tools. The increasing complexity in designs and materials is a challenge for tool manufacturers who are looking for new processes to offer more precise and reliable cutting tools.
The quality of a machined product, such as the dimensional accuracy and surface integrity, depends on many factors: for example, tool geometry, work material, and cutting conditions of the machining.
​
Dry electropolishing improves surface quality of brass instruments, avoids imperfections in the surface, while reducing time, costs and environmental impact. It precisely automates surface finishing operations, preserves geometry, tolerances and biocompatibility and extends the lifespan of brass instruments while improving the corrosion resistance.
​
This success case explains how a manufacturer of endmills improved the production capacity and quality and reduce cost of polishing of brass instruments.
​
In this document, you will learn why dry electropolishing is the preferred process for surface finishing of brass instruments.
You will also learn:
​
-
Why dry electropolishing is more effective than current methods
-
How dry electropolishing works
-
Benefits of dry electropolishing for the toolmaking industry industry
-
Cost analysis of dry electropolishing, including CAPEX and OPEX
​
Download your free copy and learn how a manufacturer of endmills improved the quality of its products and its profit.
Stainless steel buckles finishing
For the fashion and luxury industry
The company was searching for a solution to automate its hand polishing processes, with the aim of improving its productivity and achieving the highest quality in its stainless-steel buckles for belts and fashion accessories. Due to the fact that stainless steel is a hard material, polishing buckles made of this material was a high-demanding process.
​
The customer needed to polish its metal pieces to achieve a longer lifespan. Regarding the polishing target, customer’s requirements consisted in improving surface quality in polished buckles.
​
This success case explains how a renowned Italian luxury fashion company improved the quality of the products while reducing the cost and environmental impact using DLyte Dry electropolishing process. The company replaced manual polishing and outsource of traditional electropolishing only by dry electropolishing. In this document, you will discover why dry electropolishing is the preferred process for improving the surface quality of stainless steel buckles. And also you will learn:
​
-
Why dry electropolishing is more effective than current methods
-
How dry electropolishing works
-
Benefits of dry electropolishing for the fashion and luxury industry
-
Cost analysis of Dry electropolishing including CAPEX and OPEX
Download your free copy and learn how a renowned Italian luxury fashion company improved the quality of its products and increased profit using dry electropolishing.
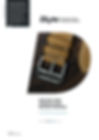