Respect the tolerances and initial shapes
Biocompatible polishing process
Increases resistance to corrosion
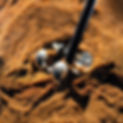
Surface finishing for the medical sector
DryLyte Technology provides custom surface finishing processes to meet stringent requirements of the Healthcare and Medical Device industry. Its applications range from grinding and deburring to surface smoothing and high gloss polishing of implants, needles, stents, medical devices and components of medical equipment which require consistent and cost-effective surface processing with high quality and leaving behind an ultrasmooth surface that impedes bacterial growth, resists corrosion and makes cleaning more effective.
The only automated system that improves quality and cost of current manufacturing processes
DLyte system innovates to improve the manufacturing process, reducing error-prone, decreasing costs and shortening lead times.
DLyte supposes a substantial improvement of quality and lifespan of medical implants responding to a demand given today’s longevity in our society.
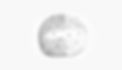
How it works
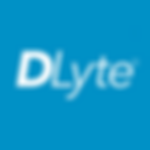
Step 1
The parts are
fixed on the holder
Step 2
The holder is
introduced the machine
Step 3
The program
is selected
Step 4
Average of 50-60
minutes per cycle

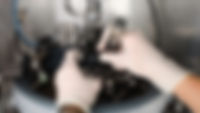
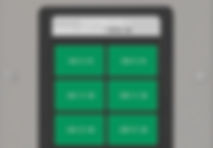
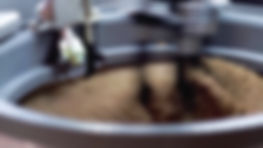

Before DLyte
60 minute cycle time

After DLyte
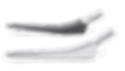
Cobalt chrome,
stainless steel, titanium and nitinol
DLyte offers high-quality finishing for cobalt chrome, stainless steel, titanium and nitinol for the Healthcare industry. required by the medical manufacturers.
The custom designed processes and media formulae improve surfaces without damaging part’s geometry and tolerances in a biocompatible process. The process ensures the repeatability and quality required by the medical manufacturers.
Respects tolerances and initial shapes
Specially effective for finishing parts with sharp edges, while ensuring the radius preservation and homogeneous result across the surface. The polishing action performed by the solid particles removing material by ion transport reaches every corner of the piece, so it can process the inner cavities which cannot be accessed mechanically.
Non-abrasive polishing
DLyte is the first non-abrasive surface finishing system able to reduce substantially the roughness. Being a non-abrasive process allows to control geometry while micro deburring or high-gloss polishing surfaces.
DLyte can achieve a high-quality finishing for machined, sintered and casted parts.



Mirror finishing in one step
The system is able to fully automatedly polishing to a mirror finish in one step. Mechanical surface finishing requires several steps to achieve mirror finishing, while liquid electropolishing generally reduces surface roughness readings of a non-electropolished surface by maximum 50%.
Precise, safe and long-lasting implants
The DLyte system based on dry electropolishing addresses the main needs of the implant industry such as shape and tolerance preservation, biocompatibility, enhances corrosion resistance, automation and reduction of complexity of current manual and multistep processes.
It brings high output with a very compact equipment, no dust and waste emissions, no need of peripheral water recycling equipment, a clean and non-hazardous process and applicable for fragile parts.
Enhances corrosion resistance
DLyte is the only system able to remove roughness and improve the corrosion resistance of the metal pieces at the same time, while reducing the number of processes required in the manufacturing process.
Corrosion is one of the main factors reducing the lifespan of implanted parts.
Most applications require a surface treatment to be performed after polishing to comply with the corrosion resistance requirements of the medical device industry.
Studies conducted show that DLyte achieves better corrosion resistance, lower surface roughness and more luster than the liquid electropolished sample.
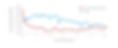
“DLyte achieves better
corrosion resistance than
liquid electropolishing”.

Proved biocompatibility
The Medical device sector requires clinically proven processes and products which guarantee their compliance with the most demanding safety regulations.
The manufacturer must ensure that the devices meet all the appropriate requirements and in particular perform a risk/benefit analysis and evaluate the biocompatibility and toxicity of the materials used.
Fragile parts finishing
Small medical devices such as stents or needles require high-quality surface finishing as micro deburring and high-gloss finishing with the disadvantage of requiring a non-aggressive process to avoid damages caused by mechanical energy. DLyte is suitable for these applications as it is an electro-chemical process which improves surfaces without mechanical action. Compared to liquid electropolishing, DLyte controls better tolerances and works efficiently at micro and macroscopic level.
Additive manufactured
implants
Additive manufacturing has been adopted by the medical device industry as it allows customization and new morphologies that were not possible to achieve with existing manufacturing technologies.


Easy waste management
and low waste and water consumption
The DLyte system does not require a closed-up system to recycle water and sludge waste treatment machinery with the corresponding space, labor, water and environmental license costs savings. The disposal of the dry electrolyte is handled by standard services.
Improvement of the working environment
The DLyte process does not require any rubber tip, electrolytic bathing or brushing, but just a simply abrasive preparation beforehand. By reducing the traditional multi-step process, DLyte improves working conditions, and drastically reduces the toxicity of the current polishing.

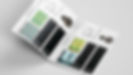